The enthusiasts of robotics, are present! Have you ever contemplated the mechanisms by which robots can perceive and interpret their environment and actions? It pertains to a concept referred to as the frame within the context of robotics. Individuals engaging with these remarkable machines must comprehend this fundamental principle of robotics.
The frame of a robot supports and structures it. Bots need it because, like the human skeleton, it gives stability and movement. One must comprehend a robot’s structure to understand its operation. It impacts accuracy, robustness, and environmental interaction. The importance of a robot’s frame will be explained in this article, along with its different types, materials, and the latest innovations in robotic frame technology. Whether you’re new to robotics or an expert, there’s something here for everyone!
Table of Contents
2. What is a Frame in a Robot?
The frame in a robot refers to the physical structure that holds together all the critical components of a robotic system, such as sensors, actuators, motors, and controllers. It provides support and ensures that all these components are aligned properly to perform the desired functions. The frame acts as the skeleton supporting the robot’s weight and maintaining its overall shape. Its design can vary significantly depending on the type of robot being created, such as industrial robots, humanoid robots, or drones.
3. The Significance of Frame in Robotics
Imagine teaching someone without markers or references. Do you realize it would be chaos? Similarly, robots require an organized way to understand their surroundings and place them in them. This is where “frame in a robot” comes in. The coordinate system, a frame-provided map, helps the robot locate and orient itself. Without a definition, the robot would be lost and unable to do its job. Robots locate themselves using their frames.
Robot Frame Basics: Position and Orientation
At its core, a frame in a robot defines two key things: position and orientation. Let’s break these down:
- 3D robot navigation relies on position: X, Y, and Z coordinates indicate its location in space. They show the robot’s X-, Y-, and Z-axis distance, height, and depth. A robot’s position may be (100, 50, or 200) on the X, Y, and Z axes.
- Orientation: X, Y, and Z-axis orientation is critical to robot design. It entails specifying how the robot rotates, like a person turning, tilting, or leaning. Angles characterize these rotations and their sequence matters. A robot may rotate 30 degrees around the Z-axis and 15 degrees around the X-axis.
How Frame in a Robot Boosts Performance
A properly defined frame in a robot is a game-changer for robot performance. It allows for:
- Precise Movements: Accurate positioning and orientation are essential for tasks like assembly, welding, and material handling.
- Simplified Programming: Working with frames makes it easier to program robot movements and interactions.
- Improved Coordination: Frames enable robots to coordinate with other machines and devices in the workspace.
- Increased Efficiency: By streamlining programming and improving accuracy, frames contribute to overall efficiency gains.
Setting Up Robot Frames: Best Practices
Setting up a “frame in a robot” correctly is crucial. Here are some best practices:
- Clear Definitions: Clearly define the origin and axes of each frame.
- Accurate Calibration: Ensure the frames are accurately calibrated to the real world.
- Consistent Units: Use consistent units (e.g., millimetres, meters) for all frame definitions.
- Documentation: Document all frame definitions for future reference.
Types of Robot Frames
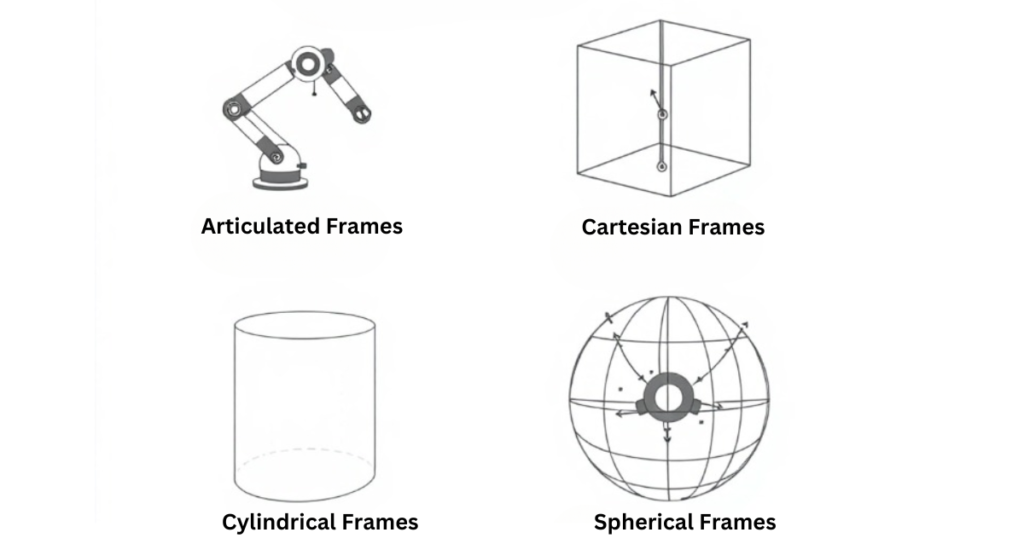
There are several different types of robot frames, each suited for specific tasks Just like robots themselves, frames in a robot come in various shapes and sizes, each suited to different applications. Here are some common types:
- Articulated Frames: These frames consist of multiple segments connected by joints, allowing for a wide range of motion, much like a human arm. These are common in industrial robots used for tasks like welding and assembly.
- Cartesian Frames: These frames utilize linear movements along three perpendicular axes (X, Y, and Z). They are often used in pick-and-place robots and CNC machines where precise linear motion is required.
- Cylindrical Frames: These frames combine rotational movement around a vertical axis with linear movement along that axis. They are often used in robots that need to reach a specific point in a cylindrical workspace.
- Spherical Frames: These frames offer a combination of rotational movements, allowing the robot to orient its end-effector in a spherical workspace.
Each type of frame serves a specific purpose, and its design must match the intended task or function of the robot.
Materials Used for Robot Frames
The choice of material for the frame in a robot is fundamental in determining its performance, weight, and durability. Some of the most commonly used materials in robot frame construction include:
- Aluminium: Lightweight, strong, and corrosion-resistant, aluminium is one of the most popular materials for robot frames.
- Steel: Steel frames provide high strength and durability but can be heavier than aluminium.
- Carbon Fiber: Known for its high strength-to-weight ratio, carbon fibre is often used in high-performance robots.
- Plastic: Used for lightweight, low-cost robots, plastic can offer flexibility but may lack the durability of metal.
The Interaction of Robot Frame Design and Performance
Robot frames are more than structural. The frame of a robot affects its speed, accuracy, and energy economy. Performance is optimized by a well-designed frame that considers weight, material, and stiffness. In dynamic circumstances, flexibility is needed, while precise jobs demand rigidity. Lighter frames offer quicker motions. Complex manoeuvres need balance and centre of gravity location to avoid tipping. Early robots’ thick frames limited usefulness. Robots with lightweight, flexible frames made of carbon fibre are more mobile and can do difficult jobs. These frame design improvements have expanded robotics applications.
Common Applications of Robot Frames
The frame in a robot is central to many industries and fields, including:
- Manufacturing: Industrial robots with robust frames are used in assembly lines for tasks like welding, painting, and packaging.
- Healthcare: Medical robots, such as surgical robots, rely on precise and durable frames to carry out complex procedures.
- Space Exploration: Robots used in space exploration must-have frames capable of withstanding extreme temperatures and radiation.
- Military and Defense: Military robots, such as bomb disposal robots, require strong, durable frames to perform dangerous tasks in hazardous environments.
Robot Frame Integration and Technological Advancements
Frames are needed to integrate sensors, actuators, and controls into the robot’s fundamental structure. Considerations like weight distribution and delicate part protection help frame design optimize component placement for best performance. Complex and customized frames may be made using 3D printing, decreasing prices and production time. Smart materials like shape-memory alloys help frames adapt to changing conditions, increasing flexibility. Smarter, more efficient, and flexible robots for numerous purposes are emerging from these developments. The robot’s capabilities and interaction with the world depend on the frame.
The Importance of a Frame in Robotics
The robot frame matters. It supports the robot’s dependability and precision, not only keeping the pieces together. Robot frames are important for several reasons. The robot frame is important for several reasons. Holding things together is not enough the robot needs to work dependably and correctly. Why it is crucial.
- Structural Integrity: The frame in a robot must be strong enough to support the weight of the robot itself, as well as any loads it might carry or forces it might encounter during operation.
- Precision and Accuracy: A rigid frame in a robot minimizes vibrations and deflections, which are crucial for precise movements and accurate task execution. Think of a robotic arm performing delicate surgery it needs to be rock solid.
- Component Mounting: The frame in a robot provides designated points for attaching all the other components, ensuring they are securely and properly positioned.
- Protection: The frame in a robot can also offer protection to internal components from impacts, dust, moisture, and other environmental hazards.
- Modularity: Often, frames in a robot are designed to be modular, allowing for easy customization, expansion, and reconfiguration.
Challenges in Designing Robot Frames
Engineers must balance several, often contradictory needs to design a robot frame. Building the robot’s performance, dependability, and safety base is more than just building a framework. Designers face several major obstacles:
- Balancing Strength and Weight: Weight and strength balance is the biggest issue. Robot frames must be strong enough to handle the robot’s weight, its payload, and external forces. Weight reduction is also important. Lighter frames accelerate, move faster, and save energy. Material selection, structural design, and sophisticated analysis are needed to balance strength and weight.
- Minimizing Vibrations: Vibrations ruin accuracy. The motor operation, fast motions, and external impacts can cause them. These vibrations might reduce the robot’s accuracy and repeatability, making precise jobs harder. Designing a robot frame with minimal vibrations requires careful consideration of rigidity, damping, and mass distribution. FEA is used to simulate and optimize the frame’s dynamic behaviour.
- Cost Optimisation: Performance and dependability are important, but cost always matters. Robot frames must be cost-effective to make, considering materials and procedures. To meet cost objectives, designers must balance performance and cost limitations by investigating new materials, production methods, and design simplifications.
Future Trends in Robot Frame Design
The field of robot frame design is constantly evolving, driven by advancements in materials science, manufacturing technologies, and computational tools. Several exciting trends are shaping the future of frames in robot design:
- Increasing Use of Lightweight Materials: The demand for lighter and more efficient robots is pushing the adoption of advanced materials like carbon fibre composites, titanium alloys, and high-strength aluminium. These materials offer excellent strength-to-weight ratios, enabling the design of lighter and more agile robots.
- Integration of Smart Sensors: Integrating sensors directly into the frame structure opens up new possibilities for real-time monitoring of the robot’s condition. Embedded sensors can provide valuable data on strain, temperature, and vibration, enabling predictive maintenance and improved performance optimization.
- Development of Adaptive Frames: Imagine a robot frame that can reconfigure itself based on the task at hand. Adaptive frames, enabled by advanced actuators and control systems, could allow robots to perform a wider range of tasks with greater efficiency and flexibility.
- Additive Manufacturing (3D Printing): Additive manufacturing is revolutionizing the way robot frames are designed and manufactured. It allows for the creation of complex geometries and customized designs with greater ease and efficiency, opening up new possibilities for optimizing frame performance and functionality.
- Bio-Inspired Design: Researchers increasingly look to nature for inspiration in designing robot frames. Bio-inspired designs, mimicking the structures and principles found in nature, can lead to more efficient, robust, and adaptable robot frames.
The frame in a robot will continue to be a critical area of innovation, driving the development of more sophisticated and capable robots for a wide range of applications.
Conclusion
The frame in a robot plays a pivotal role in determining the performance, durability, and functionality of a robotic system. Whether it’s providing structural support or enabling movement, the frame in a robot ensures that all components work in harmony. The design and material choices for the frame in a robot can make or break the robot’s efficiency, stability, and adaptability to various tasks. As technology continues to evolve, the frame in a robot will undoubtedly become more advanced, offering enhanced flexibility, strength, and sustainability. The future of robotics relies heavily on innovations in robot frame design, opening up new possibilities across multiple industries.
FAQs
1. What materials are most commonly used for robot frames?
The most common materials include aluminium, steel, carbon fibre, and plastic, with each having its advantages based on the application.
2. How does a robot’s frame affect its movement?
The frame’s weight, balance, and centre of gravity all directly impact how a robot moves, affecting speed, agility, and stability.
3. What are some challenges in designing robot frames?
Engineers must balance strength, weight, cost, and flexibility while ensuring the frame meets safety and environmental requirements.
4. Why is a robot’s frame so important?
A robot’s frame supports all its components, ensures stability, and affects performance, durability, and mobility.